Et avløpsanleggs kreative oppgradering
I mer enn 20 år stolte Gwinnett County F. Wayne Hill Water Resources Center på seks Alfa Laval Sharples DS-706 dekantersentrifuger for å behandle og avvanne biosolider i avløpsvann. Selv om disse maskinene hadde fungert pålitelig, erkjente teamet at fremskritt innen teknologi kunne tilby større effektivitet og bærekraft. Ivrige etter å utforske mer miljøvennlige løsninger, satte de seg for å oppgradere utstyret sitt, med sikte på å redusere avfall og driftskostnader samtidig som de omfavner en mer bærekraftig fremtid for anlegget.
DATO 2025-05-20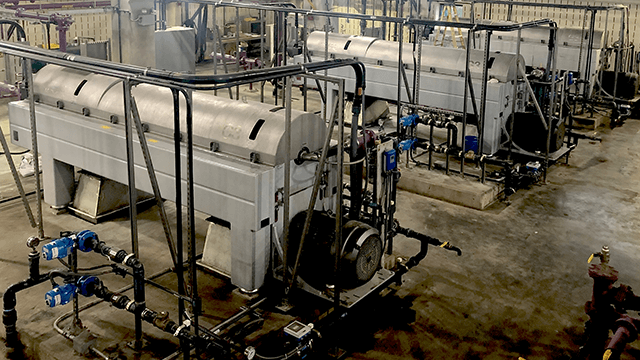
Utfordringen
Gwinnett-teamet sto overfor en betydelig utfordring – deres miljøfotavtrykk samtidig som de håndterte de enorme kostnadene ved å sende utallige tonn avvannede biologiske masser til søppelfyllinger hvert år til en kostnad av over 6 millioner dollar. Teamet trengte å finne en innovativ måte å gjøre disse biosolids, biproduktet av deres avløpsvannsanlegg, til noe verdifullt. Hvordan kunne de forvandle det som en gang ble ansett som avfall til et salgbart produkt, som gjødsel, for å redusere kostnader og bidra til bærekraft?
Løsningen
Med forståelse for prosjektets omfang, tok Gwinnett-teamet fatt på oppgaven med en langsiktig, faseinndelt strategi. Det første kritiske trinnet var å oppgradere infrastrukturen – De samarbeidet med Alfa Lavals vannteam og valgte å modernisere kontrollpanelene sine, integrere avansert logikk og innføre sanntidsovervåking og overlegne funksjoner for dekanterstyring. Disse oppgraderingene ga større driftskontroll og forbedret effektivitet, og økte tørrheten til biosolids samtidig som energiforbruket og polymerbruken ble betydelig redusert.
Et av de mest omveltende trinnene var å bytte ut 20 år gamle dekantere med Aldec G3 125-dekantere. Disse avanserte dekanterne gir høyere ytelse og effektivitet, samtidig som de bruker færre ressurser. Teamet så allerede betydelige forbedringer med installasjonen, men visjonen fortsatte.
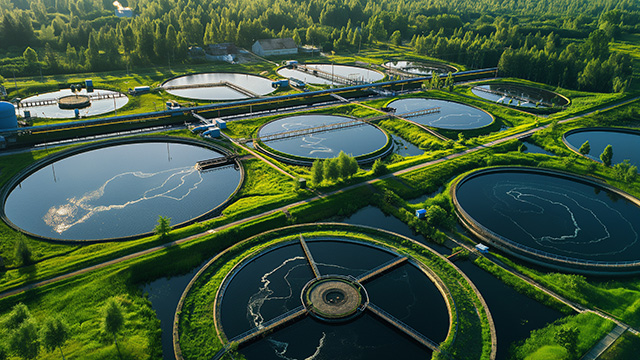
Neste trinn
Når vi ser fremover, lover neste fase av prosjektet å bli enda mer virkningsfull. Teamet planlegger å installere tørkeenheter som er i stand til å fjerne 90 % av det gjenværende vanninnholdet fra bioslam. Når det er tørket, kan det resulterende produktet selges som gjødsel av høy kvalitet, noe som gjør det som en gang var et kostbart avfallsprodukt, til en lønnsom ressurs. I tillegg til å generere inntekter, vil disse tørketromlene eliminere behovet for kostbar deponitransport, noe som reduserer driftskostnadene ytterligere.
ALDEC G3-dekanterere fortsetter å bidra i denne fasen, ettersom deres evne til å trekke ut mer vann enn forgjengerne betyr at tørkerne krever mindre energi for å fullføre jobben, noe som optimaliserer prosessen ytterligere og øker prosjektets kostnadseffektivitet.
En visjon for fremtiden
Gwinnett County legger ut på en spennende reise mot en mer bærekraftig fremtid. Deres dedikasjon til å redusere miljømessige og økonomiske konsekvenser av deres avløpsvannsanlegg er et bevis på deres fremtidsrettede lederskap. Ved å forvandle avfall til verdifull gjødsel, kutter de ikke bare kostnader for skattebetalerne, men bidrar også til en sirkulær økonomi. Dette prosjektet viser hvordan moderne avløpsrenseanlegg kan integrere innovative løsninger for å oppnå både miljømessig bærekraft og driftseffektivitet.
Gwinnett-teamets forpliktelse til å investere i nyskapende teknologi og tenke utenfor boksen er et sterkt eksempel for andre kommuner. Partnerskapet deres med teamet i Alfa Laval reflekterer et felles oppdrag om å bygge en renere, grønnere fremtid – en som kommer både lokalsamfunnet og miljøet for øvrig til gode.
Reisen fortsetter, og Gwinnett County baner vei mot en bærekraftig morgendag. Alfa Laval er stolt av å støtte dem hele veien, siden vi sammen beviser at innovasjon og bærekraft går hånd i hånd.
Resultater
Forbedret aspekt |
Før (DS-706) |
Etter (G3-125) |
Påvirkning |
Massens tørrhet |
21% |
23% |
Nærmere 6000 tonn mindre å transportere til deponi – sparer hundretusenvis av dollar i året |
Gjenvinning av faste stoffer |
~96% |
~99% |
Reduserer betraktelig behovet for å reprosessere store mengder faste stoffer gjennom systemet |
Polymerbruk |
15-17 % mindre |
~$300 000 mindre i årlige polymerkostnader |
|
Energibruk |
~45 til 50 % reduksjon |
Varierer med energikostnad og lasting, men for 6 store maskiner kan forskjellen utgjøre hundretusenvis av dollar i året |