Battery and active material production
As the demand for batteries continues to increase, new battery chemistries and production methods will emerge and commercialise in the coming years. A constant for the production of batteries and active materials is the need for efficient heat transfer and separation.
Alfa Laval empowers you to achieve:
- Boosted product recovery
- Optimized product purity
- Improved energy efficiency
- Sustainable water management
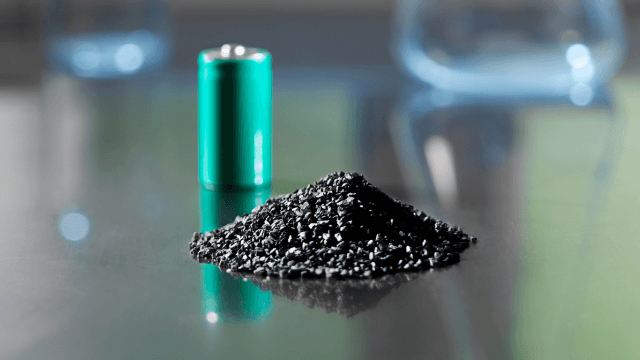
Accelerating circularity within active material and battery production
From the crystallisation of product to the wastewater treatment and impurity removal, Alfa Laval has equipment throughout the value chain that can improve processes within gigafactories and dedicated cathode active material (CAM) facilities. Through collaboration, Alfa Laval can bring both world-leading technologies and process know-how to improve processes and reduce the use of resources.
In CAM production, Alfa Laval’s evaporation systems are ideal for crystallizing lithium products and by-products, while their centrifugal separation solutions excel at removing impurities or separating crystals from liquid solutions.
Additionally, as CAM production and the production processes of gigafactories generate substantial wastewater, energy-efficient wastewater treatment is essential to reduce costs and environmental impact. Alfa Laval’s zero liquid discharge (ZLD) technology minimizes waste weight and volume, allowing water to be reused. This process often enables the recovery of valuable materials that would otherwise be lost, enhancing both sustainability and efficiency in battery manufacturing.
Process overview
The production of cathode active material (CAM) for lithium-ion batteries involves several key steps: starting with raw material preparation, where metal sulphates, hydroxides, or carbonates are processed; followed by precursor formation through co-precipitation or solid-state reactions; mixing and grinding with lithium compounds; high-temperature calcination or sintering to achieve the desired crystalline structure; purification and grinding to refine particle size; and finally, coating and calendaring to form an electrode slurry that is applied to a current collector. This multi-step process ensures the CAM has the necessary electrochemical properties for efficient battery performance and requires various separation steps and efficient heat transfer.
In a gigafactory, the production of lithium-ion battery cells involves several key processes: electrode production, where anode and cathode materials are mixed, coated, and dried; cell assembly, which includes stacking or winding electrodes with separators and filling them with electrolyte; cell finishing, involving sealing, aging, and testing the cells to ensure quality. Within the electrode production, cell assembly and cell finishing, efficient heat transfer is required. Following quality control, packaging and logistics, the water used in various production stages needs to be treatment to minimize environmental impact. Alfa Laval play a role in this by offering evaporation and ZLD technologies to lose the loop and recycle as much water back into the process as possible. This comprehensive approach ensures efficient and sustainable battery manufacturing.
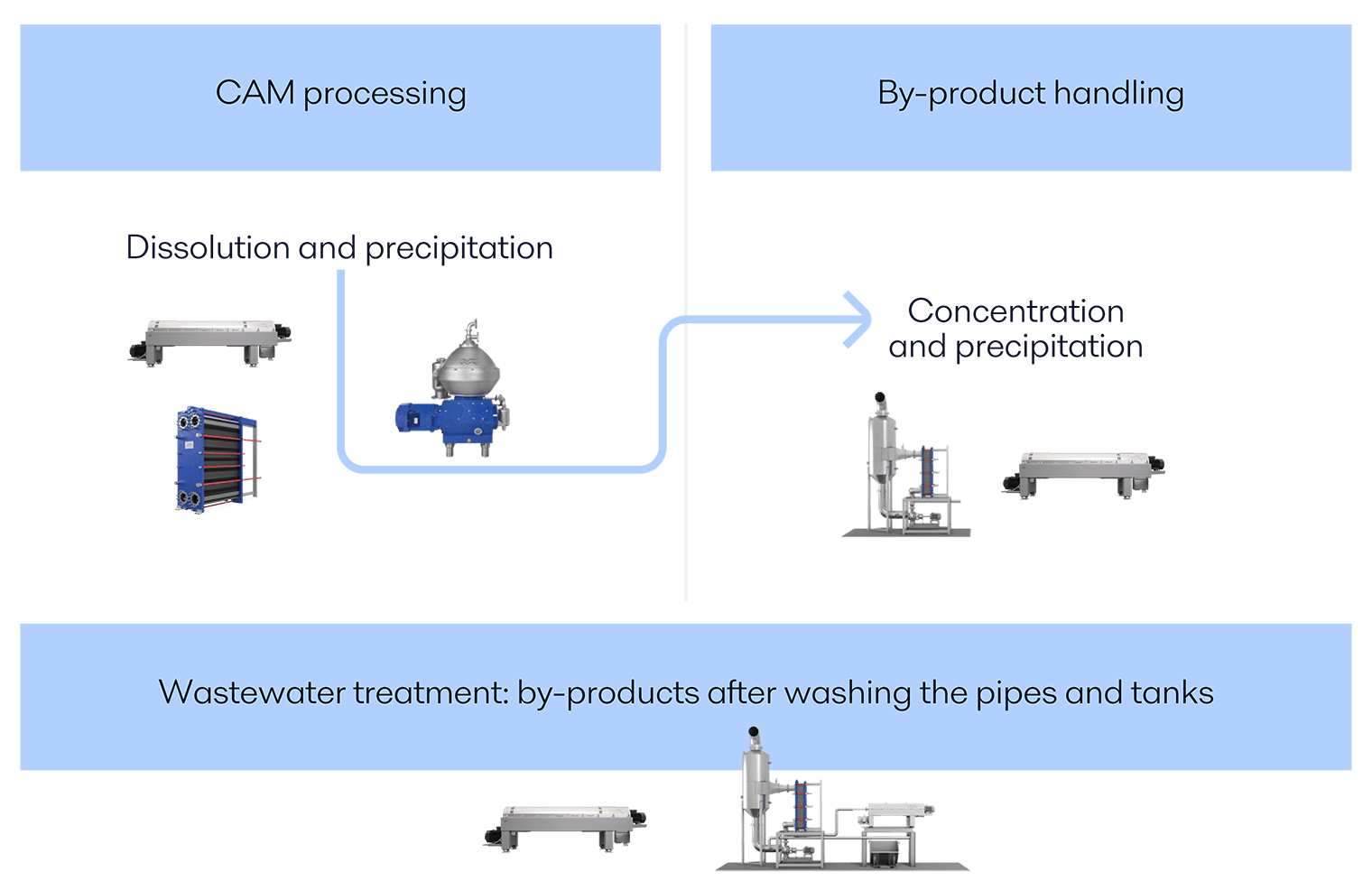
Zero liquid discharge
Alfa Laval Zero Liquid Discharge (ZLD) systems are robust, compact solutions that are used both in the main process as crystallizers and in the wastewater stream to minimize the liquid discharge.
This is made possible with the AlfaFlash evaporator that is at the core of this set up. Even when the process liquid (or water) needs removing at the maximum level, Alfa Laval ZLD can deliver energy efficient results in a smaller footprint than competing technologies.
Evaporation
Alfa Laval’s evaporators are highly efficient thermal systems that have been optimized to concentrate process liquids economically, while also preserving the quality of the final product. This is usually the case for recycling streams where the concentration of the desired compounds are very low.
Heat transfer
Alfa Laval offers a wide range of gasketed and welded plate type heat exchangers that are highly efficient, compact, and flexible in their design.
Decanter centrifuges
Decanter centrifuges provide efficient in solid-liquid separation, important for the removal of impurities in mineral refining processes and separating the recovering the final product.
Decanter centrifuges also play a key role in the treatment of the wastewater, supporting the recovery and reuse of water and other key materials.
Disc-stack separators
Disc-stack separators are reliable and highly efficient separators that can be used both for solid-liquid separation, as a polishing step after the main separation step, or liquid-liquid separation which is needed for successful implementation of solvent extraction.